Circular Process of Green Production of Technical Ceramics
Innovation represents the production process of ceramic masses, which aligns with the principles of a sustainable circular economy. This process involves reusing the raw, non-sintered waste mass, created as a by-product of technological processing, for as long as possible. This continues until the ceramic mass attains the appropriate characteristics that allow technological processing into products meeting the high demands of the customer.

| Ines Bantan Researcher |
The unsustainable linear pattern of production and consumption, which dominated production processes for many years, is not viable in the long term. Therefore, even in the production of technical ceramics, we continually adjust the organization and method of producing ceramic masses. Natural raw materials form the foundation of ceramic mass production. The natural origin is associated with altering the composition of the raw material, which is linked to changes within the deposit. As natural resources are limited, their prudent and economical use is especially crucial.
Wet grinding of raw materials in a production mill
Ceramics are the oldest man-made materials. The production process of ceramic masses is not unambiguous and varies depending on the type of technology used for ceramic product manufacturing, such as wet pressing, dry pressing, and extrusion. In our case, the process begins with the wet grinding of raw materials, followed by the homogenization of the suspension and the spraying of the granulate on the drying-spraying tower. Subsequently, it is transported to the production line where extrusion, drying, and further processing take place. The products are then hardened through sintering at a high temperature.
Homogenization of the suspension
The waste material generated in the past during the processing of sintered semi-finished products was impossible to reintroduce into the system as secondary raw material, leading to its disposal in landfills. With the advent of new technologies and procedures, there has been a shift from processing ceramic semi-finished products in the sintered state to processing them in the raw state. This results in the creation of a raw, unsintered waste mass, which is then reintroduced into the process as secondary raw material. While it comprises a mixture of high-quality natural and synthetic raw materials, its numerous parameters make it challenging to reintegrate into the production process.
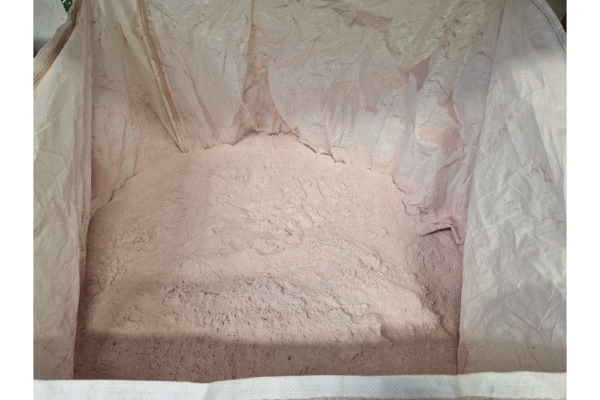 | 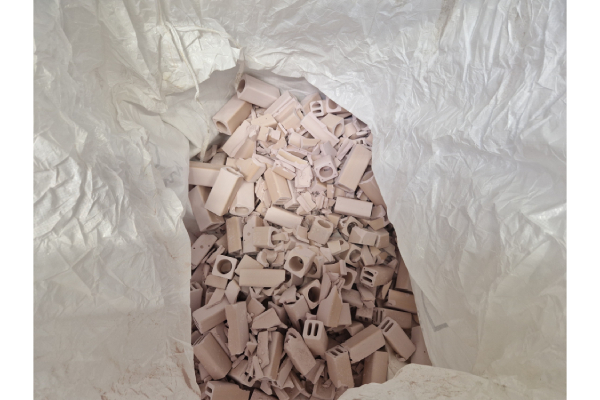 |
Secondary raw material in powder form | Secondary raw material in the form of pieces |
This is precisely why we incorporated a statistical-mathematical model to predict the quality evaluation of the mass on the extruder in the circular manufacturing process. The model relies on the measured process parameters from previous batches. Based on the characteristics of the ceramic mass on the drying-spraying tower (the most loaded and time-consuming assembly in the process line), it enables the prediction of mass quality during extrusion of products. We developed, tested, and evaluated this model in collaboration with Culmium d.o.o. within the project titled 'Determination of waste products and use of secondary materials in the industry of inorganic non-metallic materials.' We participated in the project as a consortium partner.